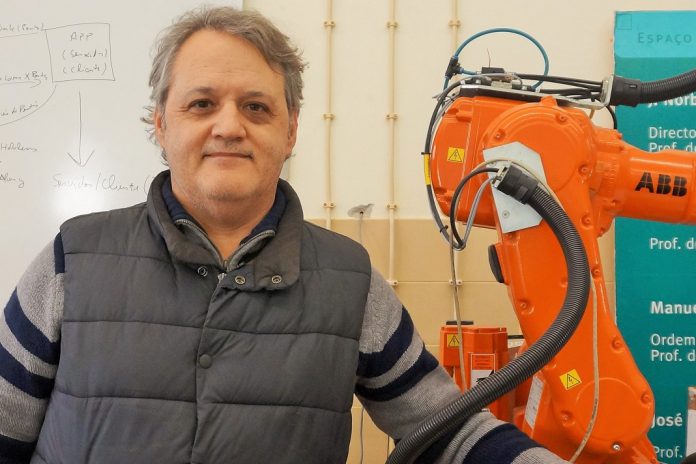
Uma equipa de investigadores da Faculdade de Ciências e Tecnologia da Universidade de Coimbra (FCTUC) e do Instituto Tecnológico para a Indústria da Noruega (SINTEF) desenvolveu um sistema robótico de impressão 3D com 6 eixos de movimento. O sistema permite a impressão de peças metálicas de grandes dimensões em vários ângulos e planos.
É a primeira vez que é desenvolvido um sistema de impressão 3D com as caraterísticas do agora divulgado, indicou a Universidade de Coimbra (UC), em comunicado, e acrescentou ainda que já levou a multinacional indiana Tata Steel a manifestar interesse pela tecnologia. A Tata Steel é uma das maiores fornecedoras de metal do mundo.
O sistema representa uma nova geração de impressão 3D para toda a indústria que utilize materiais metálicos de grande envergadura, como a indústria aeronáutica e indústria do petróleo. O novo sistema tem impactos relevantes na redução de tempo e de custos de produção.
A UC indicou que a grande mais-valia deste novo sistema robótico, além de possibilitar o dobro da performance das tradicionais impressoras 3D, que usam 3 eixos, é a sua flexibilidade, permitindo acoplar um conjunto de ferramentas, nunca antes conseguido, especialmente software de simulação em tempo real.
Norberto Pires, professor do Departamento de Engenharia Mecânica da FCTUC e coordenador do projeto, explicou: “A simulação é feita ao mesmo tempo que acontece a impressão da peça”, o que “é de extrema importância pois conduz a grandes facilidades durante toda a produção”.
“A simulação simultânea, que abrange diversas variáveis e parâmetros”, como dureza, temperatura, mudanças de fase no material, etc., “permite corrigir de imediato qualquer anomalia que possa surgir. Atualmente, a impressão é realizada por tentativa/erro até se obter os parâmetros desejados”, acrescentou o investigador.
Para chegar ao novo sistema de configuração do robô, os investigadores tiveram de estudar se a atual tecnologia robótica podia absorver um sistema com a complexidade pretendida e de seguida encontrar fórmulas “que permitissem gerar sem problemas as trajetórias de impressão para um robô de seis eixos ou mais”.
A partir da resolução do problema das trajetórias, os investigadores tiveram de “descobrir uma forma para adaptar a tecnologia de impressão existente a um sistema deste tipo – automação e integração de tecnologia”, e, por outro lado, “conseguir incorporar ferramentas de simulação que possibilitassem a correção em tempo real dos parâmetros de impressão das peças” esclareceu o coordenador do projeto.
Para levar o novo sistema ao mercado, Norberto Pires lidera agora um consórcio que junta centros de investigação da Universidade Nova de Lisboa e de várias universidades da Alemanha, Áustria, Espanha e Noruega, bem como empresas de diferentes ramos de atividade, e dado o investimento necessário exigido que é estimado em dois milhões de euros, o consórcio submeteu um projeto à União Europeia.
A investigação que levou ao desenvolvimento atual do sistema teve financiamento do programa PT2020 e por bolsas de ignição. Os resultados da investigação foram já publicados na revista científica Emerald.